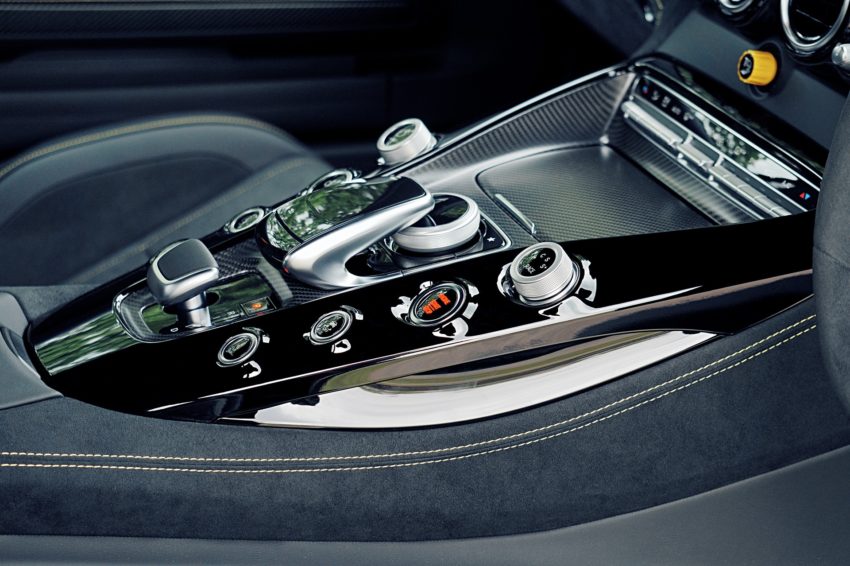
What is Isothermal Forging?
Isothermal forging is a process in which the workpiece is heated to a high temperature, then cooled rapidly to room temperature. This results in a strong, dense microstructure that is ideal for use in the automotive industry. Here are five applications of isothermal forging in the automotive industry.
Uses in the Automotive Industry
Engine components
Isothermal forging is used to produce engine components such as crankshafts, connecting rods, and camshafts. These components are subjected to high stress and must be strong and durable, making isothermal forging an ideal choice.
Transmission parts
The high precision and strength of isothermal forging makes it ideal for the production of transmission components such as gears and shafts. These parts must be able to withstand high loads and maintain their shape over time.
Suspension components
Isothermal forging is used to produce suspension components such as control arms and sway bars. These components are subjected to high stress and must be strong and lightweight, making isothermal forging a good choice.
Brake components
Brake components such as calipers and rotors are subjected to high stress and must be strong and durable. Isothermal forging provides a high-strength, lightweight solution for these components.
Drive shafts
Drive shafts are subjected to high stress and must be able to withstand high loads. Isothermal forging provides a strong, lightweight solution for these components, making it ideal for use in the automotive industry.
Conclusion
In conclusion, isothermal forging is a valuable tool for the automotive industry, providing strong, durable, and lightweight components for a wide range of applications. Its precision and strength make it ideal for use in the production of engine, transmission, suspension, brake, and drive shaft components.