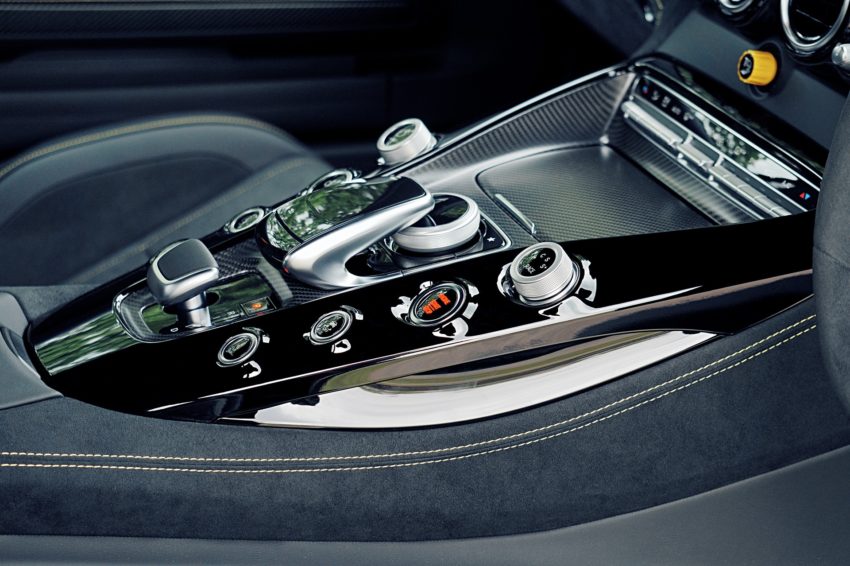
Many steps go into manufacturing a car -, the manufacturing process, in general, is quite complex. Metrology is used to measure parts with extreme precision and accuracy. When building a car, it’s sometimes difficult to tell if two parts are identical or need to be tweaked for fitment purposes. This process essentially checks to make sure all the pieces are interchangeable before they get welded together.
1. Checking for Fit
The first step in car manufacturing is to make sure all the pieces fit together. This is achieved with precision measuring instruments. Using a CMM – Coordinate Measuring Machine – with a probe, a worker can compare an item against a CAD drawing and ensure it is a perfect match. When the part isn’t exactly what is needed, You can use the machine to tweak it to not interfere with other parts designated to go together.
2. Monitoring During Production
Once the car is being assembled, there are several key areas where precision checking needs to be done. For example, if a hydraulic ram gets used to doing the assembly work, it needs to verify that the components are fitting together correctly constantly. You can do this by comparing a standard with an actual piece. Any additional tweaks needed can also be completed. Another way to ensure parts get manufactured correctly is through testing specific areas. The leader pins are commonly tested for straightness, as well as the workpiece to be welded. If they are not perfect, they can be modified so that the welding job will have better results.
3. Quality Control
Another role metrology plays is quality control before parts are shipped out. The CMM can ensure that all components meet the required measurements and perfectly fit each case. This testing will alert a worker if a part has a problem and needs to be corrected. Metrology is an important step in any manufacturing process because it ensures that all components are exactly what they should be before being put together. This ensures the final product is of high quality. If any problems get noticed, you can correct them to produce the best possible results.
4. Inspecting After Assembly
After the car is assembled, there are several areas where metrology is critical. These include a final inspection to ensure all workpieces are in good working order and subsequent quality control testing to see if any parts have come loose throughout the assembly process. This is very important because it ensures that the entire vehicle comes together correctly and will last for many years. If any problems arise, you can fix them to ensure the car lives up to its full potential.
5. Analyzing Metrics
There are so many factors involved in car manufacturing. While there are certain metrics with profitability, other metrics measure how well a car was assembled against its requirements. You can use a machine to check if parts fit perfectly and need no extra tweaking. This will alert the worker to any problems that may arise as a result. A CMM also allows for specific measurements to be taken and compared to the CAD drawing of the part in question, which is used as a standard to correct any issues before adding other components. This process ensures that cars are being manufactured correctly.
Metrology is critical in many ways throughout the manufacturing process. It ensures that every single component is correct and of the correct size. It also provides quality control during each stage of assembly, helping ensure that cars get manufactured correctly. These tools are important because they help ensure that car manufacturers are achieving optimal results.