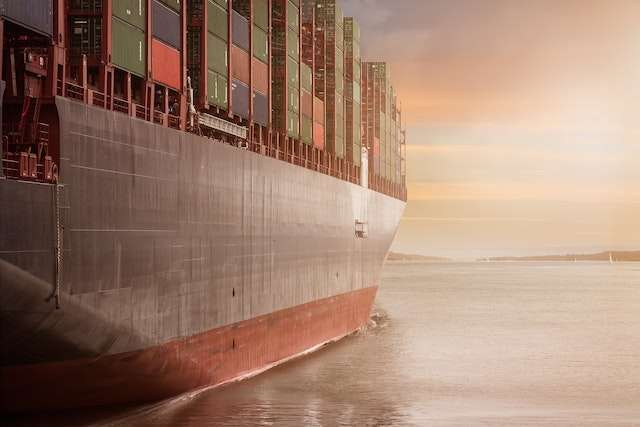
In the 2+ years since supply chains ground to a near standstill due to the coronavirus, obstacles continue to challenge shipping, transportation, and logistics companies. Though great strides have been made since 2020, disruptions persist. Moreover, the supply chain continues to be vulnerable to additional threats unrelated to the pandemic. Since there is no way to mitigate all risks to the supply chain, shipping, transportation, and logistics companies must continue looking for ways to remain competitive and grow. Here’s an overview of what we’ve learned about disruptions and how to better manage disruptions in the future.
Causes of Supply Chain Disruptions
We know the pandemic is the overarching cause of the global supply chain disruptions we’ve experienced over the past few years. But they are far from the only driving force behind hiccups in the supply chain. Interruptions to the chain may also be brought about by:
- Fuel Prices
Skyrocketing fuel prices or a potential fuel shortage could grind the supply chain to a halt.
- Natural disasters
Hurricanes, tsunamis, earthquakes, and other natural disasters frequently lead to supply chain disruptions.
- Transportation regulations
Changes in regulations can lead to delays and bottlenecks.
- Theft
For trucking fleet managers, the theft of a trailer can have a ripple effect on the supply chain. The loss or delay of cargo delivery almost always leads to delays in other deliveries as other operators and their trailers must fill the void resulting from the theft.
- Weather and Traffic
Bad weather, traffic congestion, or both can disrupt the delivery of goods and services on containers, trailers, and railcars.
- Staffing Shortages
Labor shortages also challenge the supply chain. Small shortages in staff can lead to significant delays, particularly in times of high consumer demand.
3 Ways Supply Chain Interruptions Impact Growth & Competitiveness
Supply chain interruptions cause headaches for fleet managers at shipping, rail, and trucking companies. This is because they directly impact growth and competitiveness in three distinct and interlinked ways.
- Revenue Loss
Being unable to transport goods means you lose money. Without money, there is no opportunity for your transportation or shipping company to invest in additional assets, hire top talent, or grow.
- Increased Inefficiencies
Supply chain interruptions catalyze operational inefficiencies. After all, when you cannot get the products your company needs (new trucks, trailers, parts for railcars, etc.), your team cannot do their jobs properly. This stops growth in its tracks and often leads to a decrease in productivity.
- Elevated Costs
As items become scarce due to supply chain interruptions, it is natural for companies to try to shield themselves. So, companies will order large quantities of items to ensure they don’t run out. Large orders cost a lot of money. In some cases, large orders will require that storage space be leased to accommodate them, thus further driving up costs.
Asset Tracking: The Key to Protecting Your Transportation and Logistics Company
Because there is no way to predict with any degree of certainty when supply chain disruptions will strike, trucking, shipping, and rail companies must be proactive. That means you need to invest in the technology that will help you through difficult times.
The single best way to do this is by equipping your fleet with GPS tracking devices that collect volumes of data. GPS tracking devices will give you clear, real-time visibility into the location of each asset. You’ll know when trucks leave yards, when containers leave yards, and when trailers are loaded. You’ll be able to reroute trucks around congestion. You’ll be able to pre-schedule maintenance at a convenient location along a route. Most of all, you’ll be able to make on-the-spot decisions based on data.
While you can’t prevent supply chain interruptions, you can view your company’s physical chain by being proactive and investing in the technology that provides complete visibility. This one-time investment into the future efficiency of your business will allow you to course-correct no matter what happens in the supply chain, thereby remaining competitive and safeguarding your revenue.
About the Author
Kenneth McCann is Vice President of Sales, BlackBerry Radar. To learn more about BlackBerry Radar asset tracking, or to request a free two-month trial of devices for up to five assets, contact us today at (844) 239-4527.