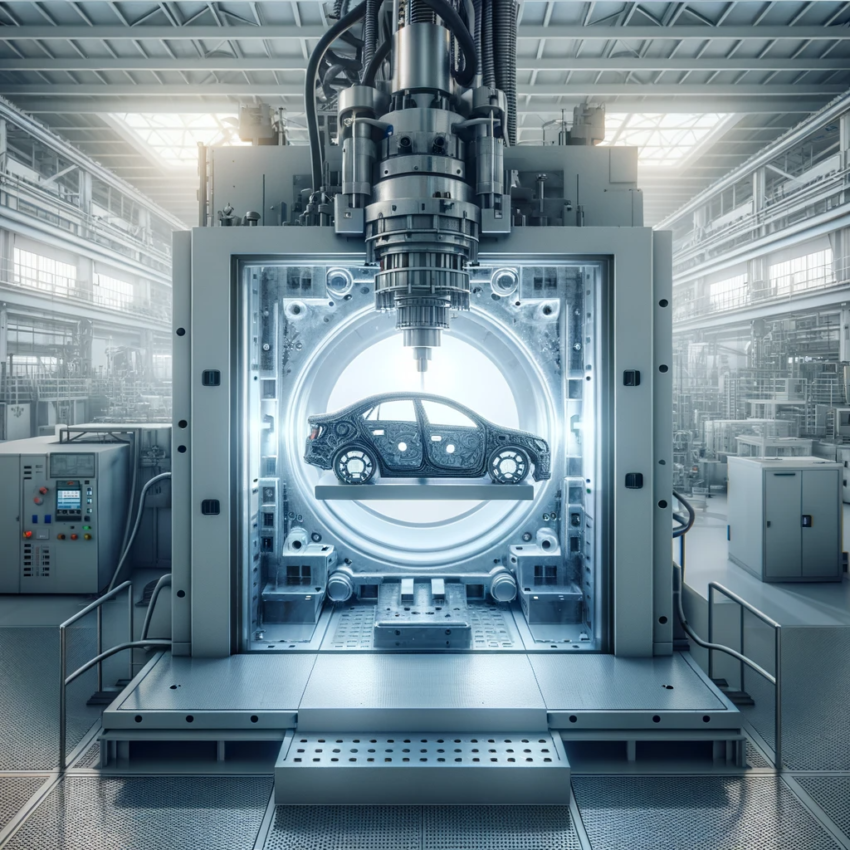
The Evolution of Plastic Products in the Automotive Industry
The automotive industry has long been a pioneer in adopting innovative manufacturing techniques to enhance the functionality, safety, and aesthetic appeal of vehicles. A critical aspect of this innovation is the production of plastic components. Traditionally, manufacturers have relied heavily on injection molding, but a new player, rotational molding, is transforming the industry, especially for companies like our client, a Canadian subcontractor specializing in plastic articles.
Understanding Rotational Molding
Rotational molding, often referred to as rotomolding, is a production method that offers significant advantages over traditional injection molding, particularly for smaller series production. The process involves a heated hollow mold which is filled with a charge or shot weight of material. It is then slowly rotated (usually around two perpendicular axes), causing the softened material to disperse and stick to the walls of the mold. To maintain even thickness throughout the part, the mold continues to rotate at all times during the heating phase and to avoid sagging or deformation during the cooling phase.
Advantages of Rotational Molding in Automotive Manufacturing
- Cost-Effective for Small Series: Rotational molding, such as the technique employed by Rotoplast, is particularly beneficial for producing small series of parts. This feature is invaluable for prototyping or for companies entering new markets where initial demand might be uncertain or low.
- Complex Shapes and Sizes: The automotive industry often requires components of complex shapes and sizes. Rotational molding excels in this area, allowing for the creation of intricate designs that might be challenging or impossible with injection molding.
The Process of Making Car Plastic Parts
- Design and Mold Creation: The process begins with a detailed design phase, where engineers and designers conceptualize the part required. Once the design is approved, a mold is created. This mold is central to the rotational molding process.
- Material Selection: The choice of material is crucial. Automotive parts require durable, heat-resistant plastics. Common choices include polyethylene, polycarbonate, and PVC.
- The Rotational Molding Process: The mold is filled with a polymer powder or resin and then heated. As it rotates, the material coats the interior surface of the mold, forming the part.
- Cooling and Removal: After the part has formed, the mold is cooled, often with air or water. Once cooled, the part can be removed and undergoes any necessary post-processing, like trimming or painting.
The Environmental Impact
Rotational molding also offers environmental benefits. The process results in minimal waste, as all material inside the mold is used in the product. Additionally, the ability to use recycled materials makes it a more sustainable option.
The Future of Automotive Plastics
The use of plastics in automotive manufacturing is a growing trend, driven by the need for lighter, more fuel-efficient vehicles. Rotational molding is at the forefront of this revolution, offering a versatile, cost-effective, and environmentally friendly solution for producing high-quality plastic components.
For further insights on how rotational molding is shaping the automotive industry, consider exploring related articles on Side CR.
External Resources and Further Reading
To learn more about the specifics of rotational molding and its applications in various industries, you can visit educational resources and industrial bodies that provide in-depth knowledge on the subject. Websites like the Association of Rotational Molders or industry-specific publications offer valuable information.